Value Stream Mapping for Knowledge Work and Services
Every organization exists to create value. Companies work to create value for customers and stakeholders. Education exists to create value for students and the community. Non-profits create value for members and society at large. Government should create value for the governed.
The creation of value is the point, but we all know that it isn’t always where we spend the bulk of our time or energy. Time, complexity, changing regulations and customer requirements all conspire to gum up our processes with activities and delays that do nothing to add value to customers. The problem isn’t that people show up to work every day wanting to spend their time on meaningless chores. Yet despite best intentions:
A bad system will beat a good person every time.
W. Edwards Deming
Running a Value Stream Mapping Workshop can help teams find and eliminate those wasteful activities that provide no value to customers nor meaning for employees.
Lean thinking has a 25-year history in manufacturing, where you can find lots of examples for how to create and use value stream maps. These VSMs illustrate raw parts arriving from suppliers, parts fabrication, movement, scheduling and factory assembly lines, packaging, shipping, and distribution channels.
In the past decade, knowledge and service organizations such as hospitals, software developers, call centers, and educational institutions have begun to apply value stream mapping to help streamline their operations and raise quality.
Lean management practices aim to bring an organization’s focus squarely on value creation by reducing costs while optimizing and improving performance. Value stream mapping (VSM) aims to depict how diverse departments within an organization combine to create value for customers.
Why Organizations Build Value Stream Maps
Value Stream Mapping makes it easy to visualize the process a company or organization uses to get “value” to the customer. The map traces the “stream” of work often from supplier to end-customer, work done both automatically and manually, inventory and information needed along the way, as a product or service is designed, produced, delivered, and serviced.
Functional teams visualize their group’s work and information flow so that everyone is able to see, understand, and improve the making of the product or service. The aim is for the lean work design to flow better for customers and become easier for employees to complete profitably and safely.
Stepping back from a value stream map, people can see a workflow and often grasp its full scope for the first time. They discover workflow bottlenecks or disconnects, and transfers between groups that hinder progress. They can identify the seven kinds of waste. They may see opportunities to help people downstream of them or inform those upstream of their needs or timing.
Nature does constant value stream mapping — it’s called evolution.
Carrie Late
Value stream mapping can identify kaizen “quick wins” that eliminate waste, outline technology projects, surface needed policy shifts, or charter new breakthrough process redesigns.
Creating a Value Stream Map for knowledge and service work requires a different approach than the VSM work conducted in a manufacturing environment. Strict measurements of time, inventory, and quality usually aren’t automatically captured as metrics for knowledge and service work as they are in manufacturing, but they may be collected or estimated. Those aspects of value stream mapping are de-emphasized here.
A VSM for knowledge and service work focuses more closely on information flow. Does the information arrive and flow in a format that all groups can use, or are there wasteful translations happening from group to group? Is missing approval or incomplete information causing delays and rework? Are there points in the flow where a lack of clear ownership or misunderstandings result in quality problems?
It takes time and collaboration by managers, experts and people who do the work to run a successful VSM workshop and even more critically, to implement the changes discovered there. That said, the benefits can be great.
How To Lead a Value Stream Mapping Workshop
This article and the attached facilitator’s guide cover how to lead a Value Stream Mapping Workshop for service and knowledge work with your team where you’ll:
- Create a value stream map, so everyone can see the value and waste in the process.
- Ensure all leaders and employees see the whole process and how their work helps or hinders other functions’ business performance.
- Identify “quick win” kaizen opportunities for reducing waste in the process.
- List on a “parking lot” the policy, systems, or leadership issues to later elevate to managers, executives, and business owners.
- Set the stage for running a future-state visioning meeting.
- Identify work centers or processing functions in need of future kaizen events.
Groups that will find this guide useful include:
- Leaders interested in continuous improvement and work redesign in mid-sized to large organizations.
- Business units where multiple departments or functional groups weave their work together to deliver a product or service.
- Those struggling to tame a variable or wasteful process and no one owns the whole of it.
- Business units preparing the launch of a new product or service that will involve multiple departments or functional groups.
Assembling the Players
VSM Workshops involve the people who supervise and conduct the functional work, the subject matter experts who support it, and may also include customers and suppliers if warranted.
Most projects like this have a champion, who will define the workshop charter and help frame the discussion, and an Executive Sponsor who commits many peoples’ time, budgets resources, and can resolve any political disagreements in order to get the value stream map and its proposed changes fully considered and the follow-up done.
Functional leads from each group involved in product delivery take responsibility for mapping their steps in one “swim lane” of the overall process for highlighting their own problems and waste and surfacing them for discussion in all other functions as well. Later, all will commit to implementing any process changes agreed to in the workshop. They may be aided by one or more additional knowledge workers or decision makers from their department.
Finally, every workshop needs a facilitator or manager with facilitation skills. This individual keeps the discussion on track, helps the group understand what to do next when they get stuck, and keeps the process moving forward. The facilitator also ensures the creation of follow-up action plans. The Value Stream Workshop works best with another dedicated individual who assists with room setup, captures notes, and keeps supplies stocked.
An Overview of the Value Stream Mapping Workshop Process
Terms to Know
If your team is new to Lean management and value stream mapping, it’s easy to get lost in all the specialized terminology.
Here’s a handy reference to terms you’ll find in this guide.
- Lean management
- Lean management focuses on optimizing the flow of products and services through the organization to maximize customer value and minimize waste.
- Current State Value Stream Map
- A Value Stream Map that shows the process as it really is, not as we say it should work or envision it could work in the future.
- Swim Lane
- A row in the Value Stream Map diagram used to separate the tasks of one functional group from another.
- Kaizen
- A change for the better; in Lean, Kaizen refers to a specific incremental change made in an effort to continuously improve the value delivered to customers.
- Burst
- A focused project around areas requiring new technology, a large process change, policy changes, or additional research.
- Future State VSM
- A Value Stream Map depicting the process as the group believes it should work in the future.
- Muda or Waste
- Activity in the process that does not contribute value to the customer. Lean practices work to eliminate 7 types of waste.
This workshop requires executive leadership and advance planning. Expect to spend several hours over the course of 3 to 6 weeks preparing for the workshop.
Phase 1: Chartering
The facilitator and the champion build the workshop charter together. This crucial first step makes sure the conditions for success are in place.
The workshop charter covers these details:
- The problem statement or need driving the workshop
- Specific goals and deliverables
- In scope and out of scope
- Level-setting requirements
- Necessary pre-work
- Attendee list
- Logistics: timing, location, deadlines, technology and/or supplies
Phase 2: Workshop Preparation
After completing the charter, the facilitator and sponsor have the information they need to begin involving attendees in pre-work.
There are 4 big preparation tasks before the workshop.
0. VSM Education
If your group is new to Value Stream Mapping, run a short introductory meeting with all workshop attendees. In it, you’ll cover:
- What Value Stream Mapping is and how your company will use it. Make sure to provide visual examples to help people “see” what the end product will look like.
- The VSM charter sheet for this workshop.
- Pre-work assignments such as preparing an overview of recent history, problems, customer feedback, metrics, etc.
Like any discipline, value stream mapping requires expertise and it’s best not to learn from initial mistakes. So if this is your first foray into lean, seek the services of an experienced lean consultant or practitioner.
1. Creation of Presentations
The workshop will begin with level-setting presentations. First, the champion or sponsor will confirm the workshop purpose, scope, goals and reasons behind it.
Often different functional groups don’t know all of what other groups do and why, so functional leads will present an overview of how their group operates. These presentations need to be created in advance, along with any other level-setting deemed necessary. They should be reviewed with the facilitator to ensure they address key questions beforehand and given a specific time limit.
2. Logistics coordination
Value stream mapping workshops work much better as face-to-face dialogues. If meeting in person, you will want to reserve a large collaborative space for the workshop. Plan a wall on which the team can build the map with all the departmental swim lanes for each functional group. It is a time saver if teams can come in and begin building their draft maps before the workshop.
If you will use an online mapping tool, set that up with swim lanes that people can populate in advance.
3. First Pass Value Stream Mapping
When you have the wall or online tool ready, invite a small group of functional leaders and select knowledgeable employees to fill out the steps in their swim lane of the overall process. Ideally, each group will fill in their tasks, decisions and inventory post-it notes before the first workshop session. This will save you lots of time in the workshop itself.
Step 3: Running the Workshop
The draft workshop agenda looks like this:
Agenda Outline
- Welcome
- Workshop Purpose (20 minutes)
- Introductions (10 minutes)
- Confirm/Present Agenda + Timings (3 minutes)
- Level Setting Presentations by Functional Leaders (if needed, MAX 15 min each)
- Populate/Confirm Swim Lanes
- Present and Critique Swim Lanes
Break
- Identify Dependencies and Discuss Solutions
Long Break
- Present Dependencies, Solutions and Counter-Measures
Break
- Final Review: Identify Bursts and Prioritize the Action List
- Final Closing
- Confirm Action Items
- Address Parking Lot
- Decide: Is a future-state VSM justified?
- Preview Follow-Up Meeting Schedule and Cascading/Reporting Messages
- Plus/Delta
This is a long agenda.
Smaller groups tackling simpler value streams should be able to complete the workshop in a single day. Larger groups with more complicated processes should reserve at least two full days to complete the workshop. You may need to break the workshop up over multiple 4-hour days.
Follow these tips to keep the schedule tight.
- Share and review level setting presentations before the workshop. Then, instead of going through each presentation when the group gets together, simply take a few minutes to address any questions.
- Ask each functional group to fill in their swim lane before the workshop in an open conference space on their own schedule.
- Work with the sponsor to anticipate breakdowns in the value stream flow and be ready to break out these trouble spots in separate sessions, either during or after the VSM meeting. If there are several smaller trouble spots, you might plan breakout sessions for the last afternoon of your workshop in order to make progress on multiple issues at once.
The facilitator’s guide explains how to lead each section of the workshop in detail, and how to manage timing.
Step 4: Follow-up and Governance
Immediately following the workshop, the champion and the assistant will collect all the workshop material and create a simple report emphasizing the follow up action commitments. Define a meeting cadence, minimum of twice a month, for the champion, team leads and responsible managers to meet and then act as “radiators” for communication.
Common Traps to Avoid
- Attempting to fix a non-operational problem such as policy, strategy or departmental conflict with the VSM. Value stream maps work for complicated problems, not complex ones.
- Fuzzy scope: trying to map a general-rather-than-specific service or knowledge work process; lack of clarity on what constitutes value or the customer requirements.
- Running a VSM without committed sponsors who will provide resources and political support.
- Mapping at the wrong level: too vague or deep in the weeds.
- Sugar-coating reality with general tasks and problems to avoid potential conflicts.
- Failing to create safety for the critique and ensuing discussion.
- Settling on improvement ideas and solutions that aren’t specific enough to be implemented.
- Too much scope; trying to “boil the ocean” during the workshop.
- Getting lost in fixing problems rather than defining project bursts for later follow up.
- Failure to follow up.
As you might expect with any process this detailed, there are challenges. Consider this a heads up; the facilitator’s guide shares strategies for avoiding these traps as you work through each phase of the workshop.
Taking the VSM Workshop Online
This workshop was originally designed for groups meeting face-to-face in a large room. If possible, I recommend working to get that in-person time. Sections of this workshop can be intense, and other parts can get boring for those not directly involved. When you have everyone in the same place, it’s easier to manage the challenging conversations and keep everyone engaged.
If that’s not possible, don’t despair. The VSM Workshop can be adapted for use with a distributed team.
First, review Lucid’s Strategies for Meeting Online When an In-Person Meeting Isn’t Possible. You can apply every strategy listed in that article for this workshop. It’s especially important to plan more work for before the workshop, and to break the workshop into shorter, focused sessions.
Next, select an online tool where you can build and critique your map. You’ll need to use a platform that will let everyone see and add to the VSM in real-time, regardless of where they are.
Software for Creating a Value Stream Map with a Distributed Team
Here are a handful of products that could do the trick:
- Realtime Board: recommended for knowledge and design workers.
- Ideaflip: recommended as a visual workshop tool to pair with more traditional management tools.
- Lucidchart (no relation!): recommended for formally documenting and collaborating on the final map. Check out their guide to Value Stream Mapping here.
- iObeya: recommended for teams using visual management to run ongoing projects.
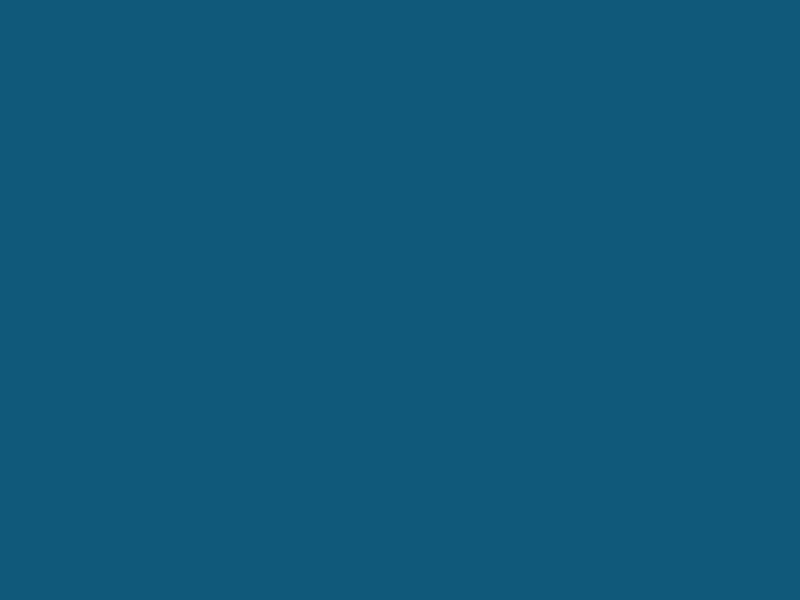
You can learn more about these products on their websites, and in our guide to online brainstorming software.
Conclusion
Value Stream Mapping can be an invaluable tool for improving a complicated process, as it removes the mystery behind how the work gets done, making it possible to create unambiguous solutions to real underlying problems.
Value stream mapping helps solve operational issues; for a problem to be addressed by a value stream map, it has to be something that can be reliably mapped! VSMs do not work well for interpersonal issues, culture issues, or in unstable situations that change rapidly.
This guide shows one way to run a VSM workshop. If you try this with your team, please let me know how it works out! I’m also available to answer questions or provide coaching. Leave a comment below or reach me directly using my contact information at the end of the facilitator’s guide.